Application Areas
Application Industry
Application Industry
Industrial silicon
The silicon plant's blast furnace flue gas treatment project uses a highly efficient calcium-based dry desulfurization agent to achieve the synergistic removal of multiple pollutants such as SO2, NOx, and particulate matter in the flue gas, improving the quality of flue gas emissions.
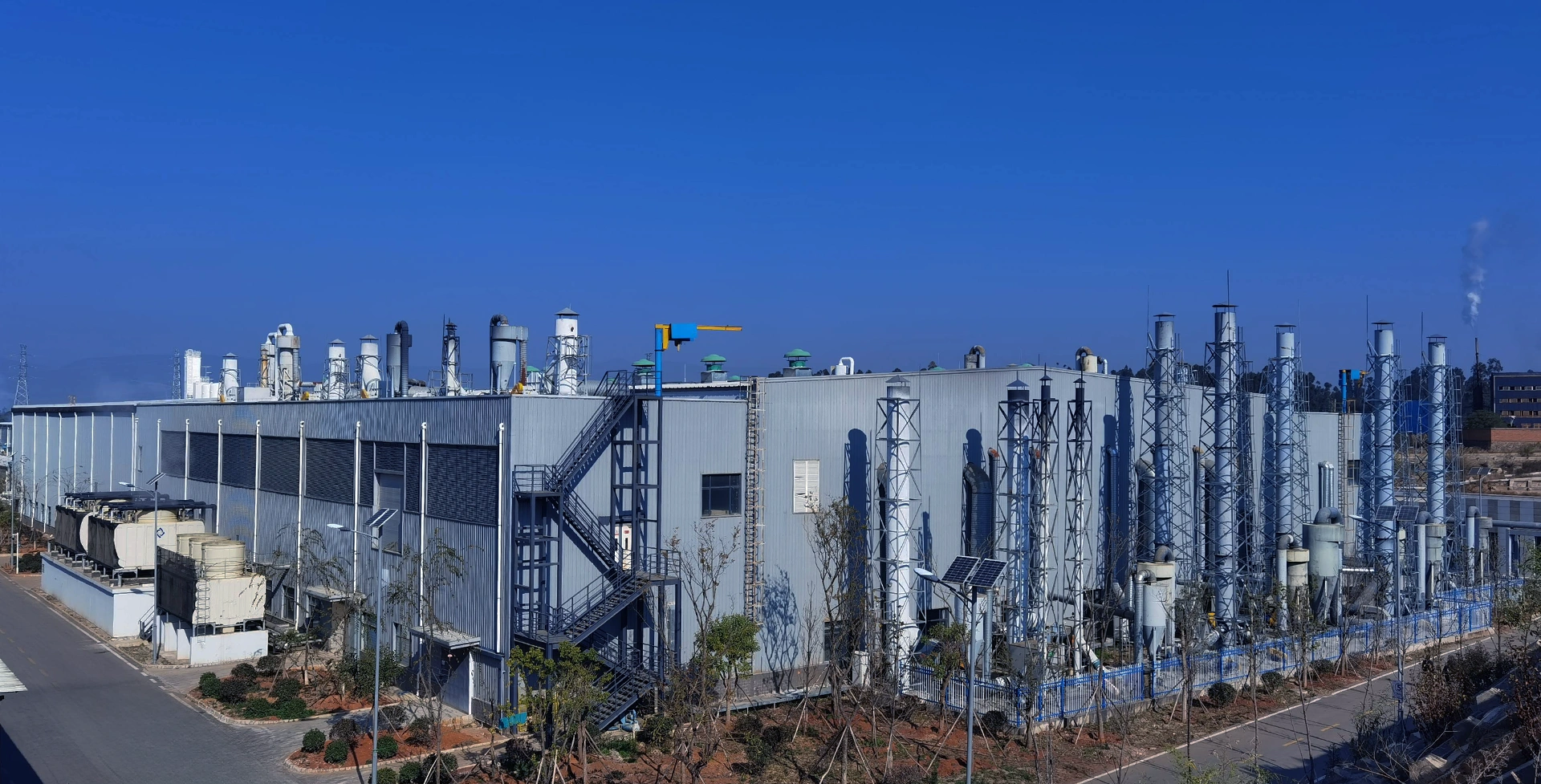
Efficient calcium-based desulfurizer dry desulfurization process
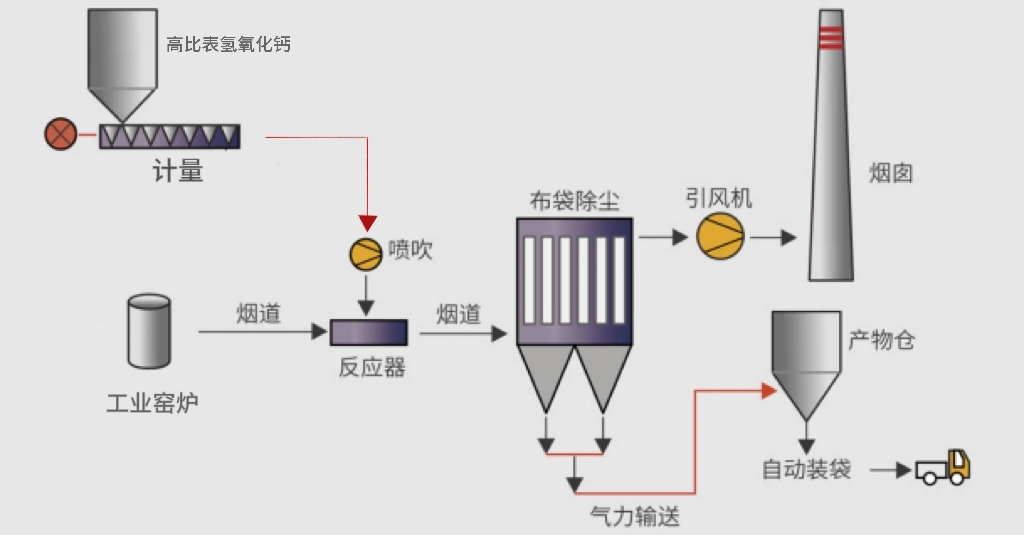
Desulfurizing Agent System
This system mainly includes unloading, powder silo, metering module, and conveying system. High specific surface area calcium hydroxide powder is sent into the powder silo from a ton bag via an electric hoist, and then through the metering module at the bottom of the powder silo, it is conveyed to the desulfurization flue or desulfurization tower via a blower.
Desulfurization Reaction System
This system mainly includes the desulfurization flue or desulfurization tower. The high specific surface area calcium hydroxide powder is injected into the desulfurization system, where it undergoes a neutralization reaction with SO2, thereby removing SO2 and generating reaction products such as CaSO4 and CaSO3. These dry products enter the baghouse dust collector with the flue gas.
Desulfurization Product Collection
This system mainly includes a baghouse dust collector and desulfurization product collection. The gypsum powder generated after desulfurization is collected by the baghouse dust collector after dry desulfurization, and is centrally processed together with the dust through the ash conveying system. The main components of the desulfurization products are CaSO4 and CaSO3, which are not hazardous waste and can be treated together with ordinary dust. The baghouse dust collector can ensure that the dust concentration in the flue gas is within the design index.
COOKIES
Our website uses cookies and similar technologies to personalize the advertising shown to you and to help you get the best experience on our website. For more information, see our Privacy & Cookie Policy
COOKIES
Our website uses cookies and similar technologies to personalize the advertising shown to you and to help you get the best experience on our website. For more information, see our Privacy & Cookie Policy
These cookies are necessary for basic functions such as payment. Standard cookies cannot be turned off and do not store any of your information.
These cookies collect information, such as how many people are using our site or which pages are popular, to help us improve the customer experience. Turning these cookies off will mean we can't collect information to improve your experience.
These cookies enable the website to provide enhanced functionality and personalization. They may be set by us or by third-party providers whose services we have added to our pages. If you do not allow these cookies, some or all of these services may not function properly.
These cookies help us understand what you are interested in so that we can show you relevant advertising on other websites. Turning these cookies off will mean we are unable to show you any personalized advertising.